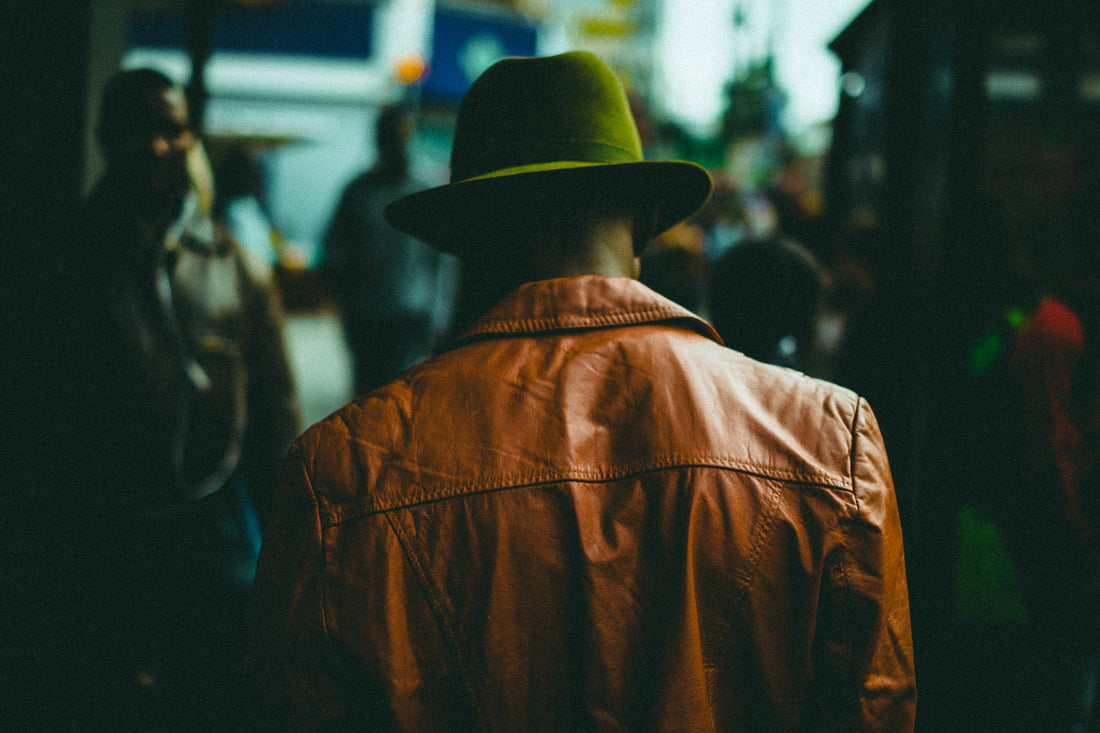
What Material & Methods Are Used In Making Leather Jacket
Various animal skins are used to make leather jackets; cowhide is the most common material for heavy-duty jackets, although buffalo and horse hides are also utilized. Although more exotic leathers like kangaroo are also utilized, sheep, pig, or goat hides are often used to make lightweight leather jackets.
Using Material in Making Leather Jacket
The materials used to make leather jackets include the following:
1. Unprocessed Materials:
Typically, hides from antelopes, buckskins, lambskins, sheepskins, and cows are used to produce leather coats.
At the meat processing facility, the animal's skin is immediately salted, chilled, or placed in barrels of brine. After that, it is taken to the tannery, where the skins go through several procedures meant to soften and preserve the hides. To ensure that the finished garment is of the highest caliber, the work done in the tannery is crucial.
2. Sewing Materials:
Typically, the clothing manufacturer purchases and stores items like thread, lining, seam tape, buttons, snaps, and zippers from outside vendors.
The Method of Preparation
1. Cleaning and Trimming:
Size, weight, and thickness-based trimming and sorting are done to the skins. Any leftover proteins that can encourage the growth of germs must be eliminated. To do this, the skins are submerged in water, detergents, and bactericides in rotating drums. Lime solutions or chemical sprays are used to get rid of hair. A scudding machine with dull blades removes any superfluous hair.
Before the hides are soaked in an acidic solution and subjected to an enzyme procedure called bating, which further eliminates the collagen from the skin, another round of washing (de-liming) eliminates these chemicals. Lastly, sulfuric acid and salt are pickled with the ski
2. Sun Protection:
There are three different methods of tanning the skin. The longest process is vegetable tanning, which involves soaking the skins in increasingly powerful tannic acid solutions for many weeks. On the other hand, soaking time for some delicate leathers, like lambskin, can be as little as 12 hours.
Although mineral tanning is more quicker, it might alter the leather's color. Using this technique, the skins are put inside drums filled with alum salt and paddles that constantly agitate the contents.
3. Sanitization and Cleaning:
The skins are carefully wrung out and given another wash once they have been tanned. The skins are then put on conveyor belts that transport them to drying tunnels after being sliced to a consistent thickness with a band knife. Stretching the skins on frames usually stops them from shrinking while they are drying. The hides are treated with water and soap and let hang for a while to help prevent the rigidity that drying causes.
The purpose of the machinery used to handle the leather regularly after it has been conditioned is to further loosen and increase the flexibility of the fibers. The skins are hung in cabinets with vacuum drying during the last drying stage.
The Method of Production:
The appearance of conventional sewing factories, where one worker would have worked on a single garment from start to finish, was altered by the invention of high-speed sewing technology. Since leather clothing is regarded as a luxury good, many buyers still choose hand-made goods made by really talented artisans. Nonetheless, factory mass manufacturing follows these processes.
1. Design of Jackets:
Designers are usually employed by garment manufacturers to generate patterns that are used to make apparel. The designs are rated by computerized devices using government anthropometric charts, which allocate sizes depending on weight and body height. After that, the computer generates the original design's patterns in various sizes.
2. Pressing and Forming:
The animal skins are turned into jackets using a series of pressing techniques that include applying heat, steaming, and blocking. Whether the jacket is designed in the bomber or blazer style, the unique form is achieved using buck presses that are outfitted with gauges and controllers to manage the amount of steam and pressure.
Heat is then applied after curved blocks have been positioned around the collars and cuffs. The cuffs and collars remain bent once the blocks are removed.
3. Last Examination:
Before a jacket is shipped from the factory, it is manually examined. After finishing, the jackets are placed into cartons, wrapped in plastic bags, and sent to the merchant.
CONCLUSION:
Although leather jackets are a popular choice due to their durability and design, it's also important to consider the lining material. The jacket gains structure and weight from the lining, which also gives it warmth and a polished, silky appearance.
The lining also adds longevity to the jacket by hiding interlinings, padding, and rough edges. When choosing custom-made apparel, it's important to take into account the different possibilities for lining materials when wearing a leather jacket.
Getting a jacket with a bespoke lining is the best method to show off your unique style. You may select from an array of materials and hues for the interior of your custom jacket at Lusso Leather.
Read More:
- Why Leather Jacket Is So Popular?
- Top 5 Major Colors of Leather Jackets
- Top 6 Benefits of Full Grain Leather Jacket